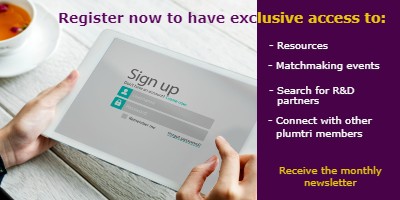
Register on plumtri as an Individual or as an Organisation to gain access to all of its useful features and remain updated on the latest R&I news, events and funding opportunities.
Composite materials are made up of two or more distinct constituent materials encapsulated together that when combined develop a new material capable to take advantage of the individual material properties of the constituent phases. Concrete which is heavily used in buildings is a composite material in itself, made up of aggregate bonded together with cement. The relatively low tensile strength and ductility of concrete can be enhanced further by the inclusion of steel reinforcements leading to a fibrous reinforced composite material. Various fibrous reinforced composites have been developed in the past century. Primarily the use of glass fibres embedded in a polymeric matrix better known as fibre glass has found their use in various industries such as the marine industry. Composite materials have the potential to replace steel in the automotive industry by reducing the total weight of a vehicle by around 25%. The use of composite materials in the aerospace industry has dramatically increased from 1% in the Boeing 747 during 1979 to 50% in the Boeing 787 by the year 2011, enhancing the efficiency of the aircraft and saving fuel. Composite material in general are lighter, chemically resistant to corrosion and can be designed to provide structural strength along a particular loading configuration, often exceeding that of alloys. They are the materials of the future with endless combinations and possibilities.
The relatively higher strength attained in fibrous composite materials result from the strength and stiffness of synthetic fibres such as glass or carbon fibres that are eventually embedded in a polymer matrix to be able to transfer load from one fibre to another. The growing use of composite materials has revolutionized industries by offering lighter, stronger alternatives to traditional materials, enabling more efficient machines and new technologies. However, these advancements have come with significant challenges, particularly in terms of energy consumption and sustainability—both of which are crucial concerns in today’s environmentally conscious world. Synthetic fibres and resins, cannot be recycled or easily disposed and effectively are not carbon neutral. Furthermore, resins are generally derived from the petrochemical industry that can also be carcinogenic during the production process. The development of natural fiber-based composites presents a promising solution. Bio-composites, which bridge the gap between synthetic composites and unreinforced plastics, offer significant potential for applications ranging from eco-friendly vehicle furnishings to sports equipment and prosthetics. Their customizable properties through hybridization enhance both performance and aesthetics while reducing post-processing. The synergetic collaboration between the University of Malta and Zhejiang Sci-Tech University in China through the SINO-Malta 2022 ECO-Composite project set out to develop an Ecological Natural Fibre Reinforced Composite solutions. The project aims to develop an eco-friendly composite material made up of natural fibres embedded in a bio –based resin. Natural fibres have different mechanical characteristics but are relatively weaker than synthetic glass or carbon fibre composites unless they are not appropriately fabricated and embedded in the right matrix. In this project natural fibres derived from the locally grown Agave Sisalana plant (Sisal) and the abundant Linseed (Flax) found worldwide (Figure 1) will be used and together with a bio-based epoxy resin, the optimal ecological fibre reinforced hybrid composite will be developed.
The production of the sisal/flax bio-composites is a potential bridge between the high strength synthetic fibre reinforced composites and the commonly used unreinforced plastics. The novel bio-composites would occupy a space within the industry that will greatly benefit well established sectors such as the automotive and sports and boost new producers and markets. The application of low cost, low environmental impact and tailored natural composite could provide a more sustainable growth in the composite manufacturing industry. Indirectly, the focus on greener production of vegetable fibres involves a broad process from the farmer to fibre processing industries, generating jobs and opportunities. Furthermore, the development of these industries drives further research into natural fibres, such as utilizing two or more fibres within the same structure to enhance and tailor their characteristics.
The combination of hybrid composites using different natural fibres is still in its infancy. Hybridisation can be attained by fabricating mats consisting of different ratios of sisal and flax fibres along the wrap and weft direction or even through the sequential placing of a combination of fibre yarns in a uniaxial direction to produce what is known as intraply laminae as shown in figure 2 and 3. The different fibres can also be spun together to develop an intrayarn fibres that can also in turn be woven into a unidirectional or biaxial mat. The challenge here is to spin a relatively thick, longer and abrasive sisal fibre with short, thinner flax fibrils. Another option of braiding sisal and flax yarns using different fibre ratios is also being investigated.
While the reinforcing agent of composite materials is attained through the structural stiffness of the fibres, the fibres need to be adequately embedded in a matrix that provides a medium to transfer the loads from one fibre. It is therefore important that good fibre/matrix adhesion properties are achieved. The cellulose and hydrophobic properties of natural fibres presents a challenge. The project looks at different natural fibre surface modifications by developing a newly designed resin based blend to enhance the adhesive properties between the fibres and the matrix. Bio resins have a low glass transition temperature, are relatively weak and take long to cure unless they are properly synthesized with other polymers and materials. A new systematic synthesized bio-based resin is being developed that not only has a higher structural strength but cures faster and provides the ultimate viscosity properties to be able to resin infuse the mats. The optimal fabrication route based on temperature, releasing agents and additives will be identified through a series of mechanical tests to establish the tensile, compressive, shear and impact properties of the newly design bio based resin.
The constituent natural fibre mats and bio-based epoxy will be used to manufacture sample specimens using the resin infusion process as shown in figure 4. Different volume fraction and fibre orientations will be investigated. The static tensile, compressive, shear and flexural material characteristics of the different specimens will be identified through a series of experimental tests by means of a universal testing machine. The tensile properties in the fibre and matrix direction will be identified following ISO 527 standards. The IITRI compression fixture will be used to establish the compression material properties as per ISO 14126 standard. The V-notched beam, Iosipescu test method will be used to identify the shear properties, while the three-point bending flexural test as per ISO 14125 will be adopted to find the flexural properties of the specimens. The results will be used to populate a meso-scale numerical model that is capable of analyzing and identifying the best fibre ratio, hybrid composition and orientation for different loading configurations.
Project received funding from Xjenza Malta and the Ministry for Science and Technology of the People’s Republic of China (MOST), through the SINO-MALTA Fund 2022 Call (Science and Technology Cooperation).
Download the orriginal article from below.
Information and images source: